Rollers For Paper Industry
Premium range of covering compound
Paper Industry
We at ZENITH manufacture OEM-grade rollers catering to the paper industry. Which are based on roller operating parameters. Our roll technology involves the manufacturing, covering & servicing of large metal rolls (Up to 10 metres. Long, 2 MM in Diameter & 50 Tons weight), which are manufactured, covered, and serviced using roll technology. Application, chemistry, speed, temperature, pressure, roll geometry, deflection, balance, and coefficient of friction are all factors that influence roll quality.

Among our offerings are:
- Rubber Covering
- Re-Grinds
- New Core Design & Fabrication
- Core Repair
- Ultrasonic test & Balancing machine
- Crowning
- Grooving
- Engineering Services
- Extensive Field Support
Delivering Dynamic Solutions
Modern paper machines are built to manufacture/produce more at a faster rate. We have rubber-covering options that allow for optimum load usage without risk of crushing, as well as maximum covering resiliency, even at increasing hardness, to maintain a consistent Nip Zone.
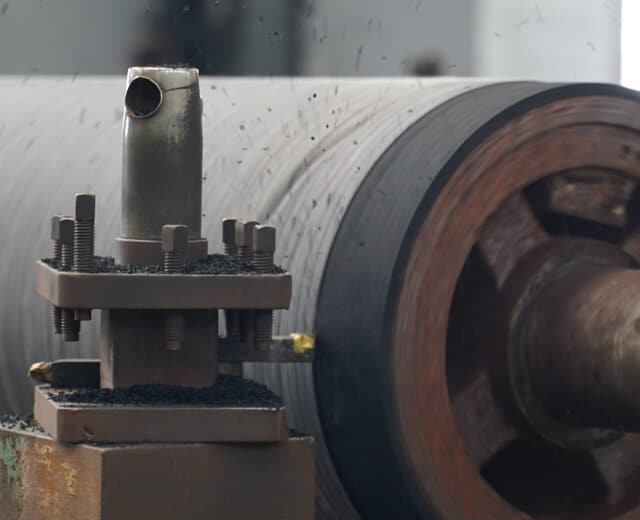
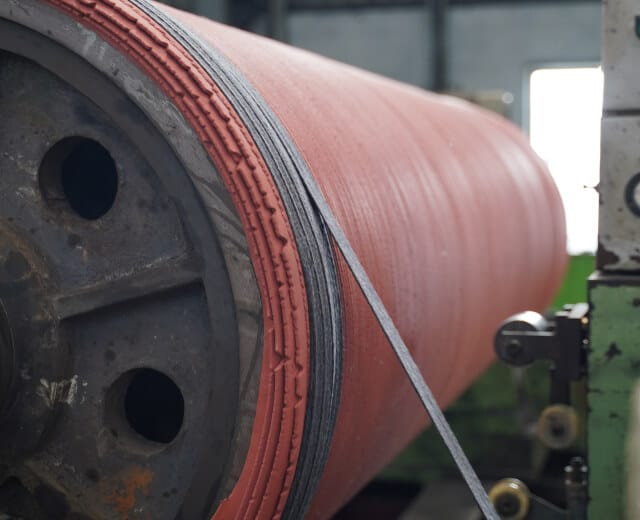
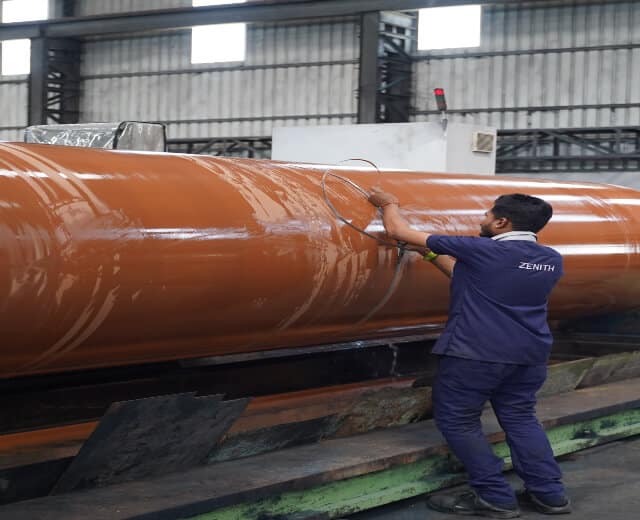
Specialised Coverings:
Polyurethane (PU)
The PU Covers are made from the most modern polymers, specially designed for the demanding conditions in paper machines. Our special coverings are mostly suitable for different types of Press & Size Press Rollers.
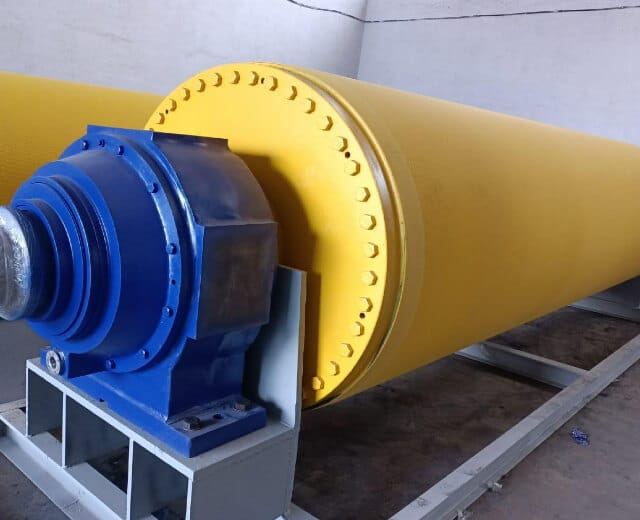
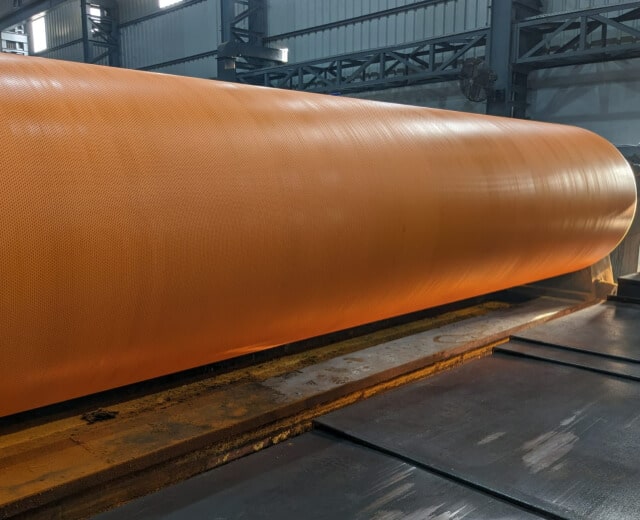
Super Flex (Hybrid Covers for Press Section)
Superflex BD is a special hybrid compound developed with Italian technology. It is made out of specialised rubber & polymers to achieve better and wider NIP, dewatering, high linear load, and much better resilience as compared to normal rubber covers.
Superflex Size/Rock is a special hybrid compound made up of Italian technology which can resist starch, oil, solvent, and sizing chemicals. It is very effective in starch slurry.
Composite Covering
Zenith Launches Nanotek & Nanorok Compoisite Compound. Composite calender covers are made of modern fiber reinforced compound. Special fillers ensure the optimal hardness, robustness and surface smoothness.
Advantages are depending on the existing situation and previously used roll covers:
• Improvement ofpaper quality
• Avoiding of paper blackening and paper mottling
• Higher bulk ofpaper
• Lifetime ofcover
• Marking resistance
• Allowing higher speed and load on machine
• Less downtime ofmachine
• Allows continues doctoring
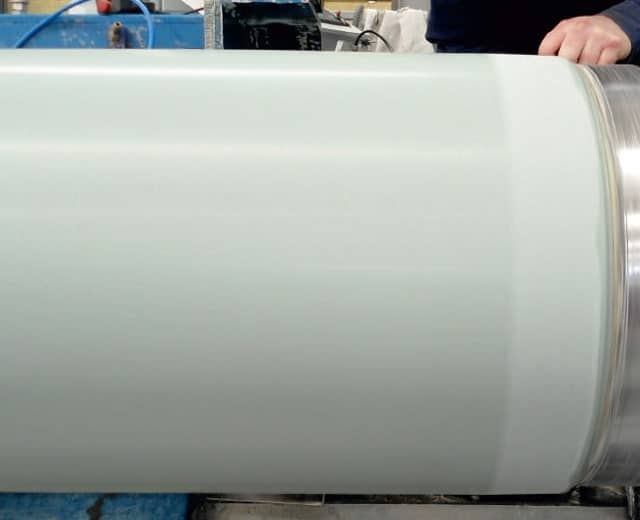
Nanotek and Nanorok have been designed for soft calendar presses and hard presses, respectively. With features like resistance to wear and chemicals, their use increases the life- span ofthe calendars along with a number of other benefits for its users.
1. Nanotek has the ability to withstand exacting working conditions for the soft calendar presses including — soft calendar, super calendar, multi-nip calendar, and mat on line calendar. Thus, it makes for a great choice of composite covers. Since the raw material used and the method of manufacturing results in an exceptional quality of finishing, there are no differences in surface texture or in processing paper. Due to low level of porosity of Nanotek, achieving excellent surface finishing is albeit easier. Moreover, the cover has excellent wear resistance ensuring the durability of the calendar.
Nanotek is recommended in the following positions.
• Soft Calender
• Mat-On-Line Calender
• Multinip Calender
• Super Calender
2. Nanorok is a composite cover for hard presses, which can also operate effectively in the most demanding operative conditions. It is recommended for a range of presses, including — hard press (wet environment), central press, hard-size press, and shoot press. The raw materials used as well as the efficiency in manufacturing enables the user to get a very good finish in their products. With this cover, all types of blades can be used while the life span is also increased and the good condition of the surface roughness and the press is maintained. Moreover, Nanorok is resistant to a number ofchemicals which are commonly used in the pulp, paper, and paperboard industry, including alcohol, acetone, acid chemicals, etc. It is also resistant to short exposures of oil and diluted caustic solutions.
Endowed with the ability to improve resistance to abrasion, it can significantly increase the lifetime of the presses.
Nanorok is recommended in the following positions.
• Hard Press (wet environment)
• Central Press
• Shoot Press
• Hard-Size Press